"Test #2" -- Presentation Day
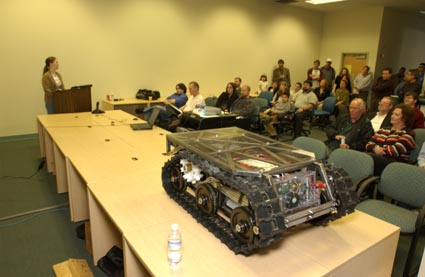 |
Major Test #2: 04.08.2005
Test Objective: Final presentation.
Duration: Half an hour, roughly five minutes of driving
Result: A very impressive presentation despite several problems (We got an A+). Second massive controller failure (not until after the presentation, thank God).
Bottom Line: Over $800 in replacement parts necessary (not counting refunds)
Media: 22 images
|
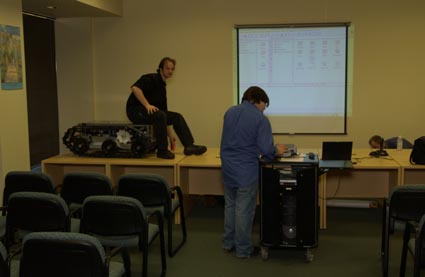 |
It's the big day, April 8th, and we're scheduled to be the first presenters of this term's Senior Design Project final presentation day for the engineering and science departments. The new speed controller (the replacement for the one we blew up during the last test) got here 28 hours ago, but we managed to get everything wired back up and working with time to spare. We drove it out of the car, through the halls, and into the presentation room. Getting it up onto the table was a little sketchy, but we managed it without killing anyone (just barely). Here you can see me having a Coke and lounging on the robot while Jake Deyo, the lab manager at Cogswell, gets the projector set up. Thanks for all your help Jake! |
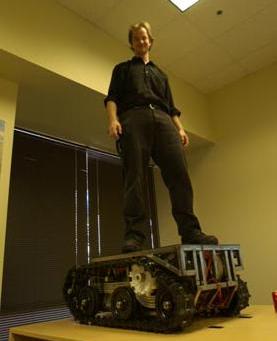 |
The school brought in a photographer for the presentations to get some good pictures for promotional reasons. Steve Hartson of Hartson Photography came by to oblige. He did a great job, and all of the pictures on this page are courtesy of him. He even provided the low-res, unbalanced versions used here to me free, which was great seeing as I just spent all my money on robot parts. Thanks Steve! |
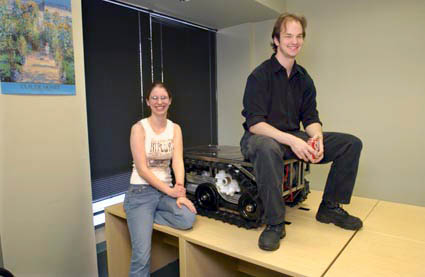 |
This is just a little "before" picture. We're all set up and ready to go, so now we just have to wait until the crowd shows up. For this picture, Steve took a few minutes to balance the colors for me (compare to the picture above). The flourescent lighting in the room makes for some strange colors on film (the slight green tint in many of the pictures). Normally, he would provide a full package of really nice large, hi-resolution, color balanced files, but because Cogswell has a big Digital Arts department, he usually cuts us a deal and lets some of our more talented students do the balancing act for him. Anyway, if you actually hire the guy, you'll get nice clean results like in this picture. If, on the other hand, you're looking for free handouts like I was, well, you get to put up with a little green around the edges. |
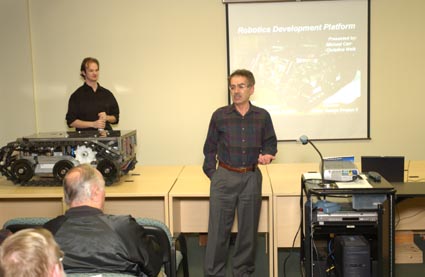 |
This is Dr. Pashin Nikaaien, our mechanical engineering advisor for the project, introducing us. |
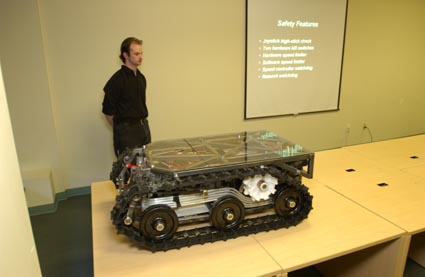 |
Here we're presenting away. The first portion of the talk was delivered by Christina (not pictured here), and covered the general project overview, input specification, safety features, and software design. |
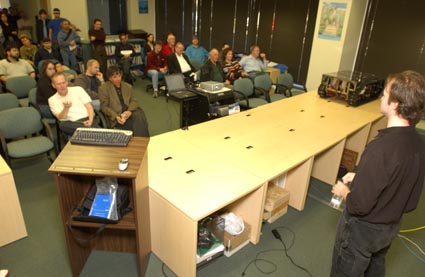 |
The second portion of the talk was delivered by me, and covered the actual build process (it was essentially an incredibly brief mention of the major points presented on this website). As you can see, the crowd isn't a particularly big one. The front row sort of cleared out once they realized that I was going to want to drive a 400 pound robot on the table tops just a few feet away. About half the audience ended up standing in the back. In the front row on the left you can see our computer science advisor Professor Gordon Jenkins (in white) as well as the College's Provost Dr. el Hadi Aggoune (in olive). |
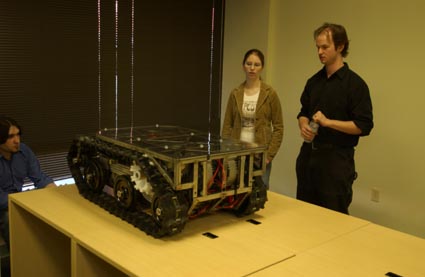 |
With the conclusion of the talking points of our presentation, we planned to move into a brief demonstration followed by questions. Rather than wait for the on-board computer to boot up, we left it on during the talk so that we could dive right in. Unfortunately, we underestimated the idle current draw of the system, and when it came time to establish the connection we had already depleted the computer batteries so far that it had shut down the wireless card. This was bad news. We decided to field a few questions while Jake ran to grab a few alligator-clip leads from the electrical circuits lab so that I could hot-wire this thing. |
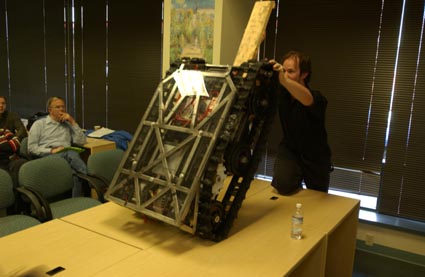 |
A little peek under the "hood". |
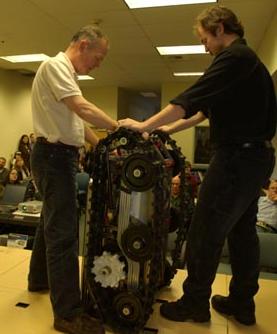 |
Professor Jenkins is here helping me steady the robot so that I can get to the necessary battery terminals. At this point, I was really wishing that I'd just left the Lexan plates at home: they made my life much more difficult. |
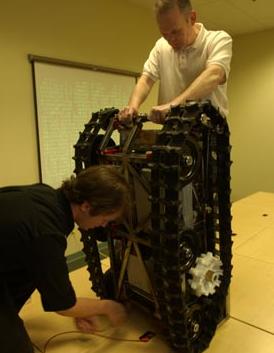 |
This is why having someone on hand to help is very nice. The robot does balance in this position, but when you're the one working under it, it starts to look really unstable. |
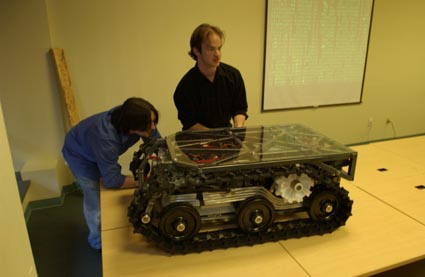 |
Here I'm wiring the other connection and fielding build questions at the same time. This would have been a snap without the Lexan plate, but instead of just reaching through the top I had to squeeze in through the tracks on the side. There wasn't enough room to open the alligator clip on the wire, so I just had to wedge it in under the ring terminal and hope it held. It actually worked rather well. |
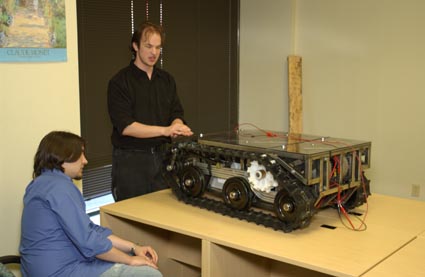 |
You can see just how professional the hot-wiring looks. Sure, it's trailing wires on the table and going over a bump is likely to disconnect the computer's power lines, but it'll work in a pinch (and we were in a pinch). |
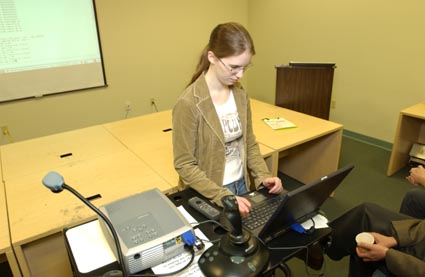 |
Finally, we were ready to start the demonstration. Here, Christina is explaining the user interface and login process using the Fedora Core 2 laptop. |
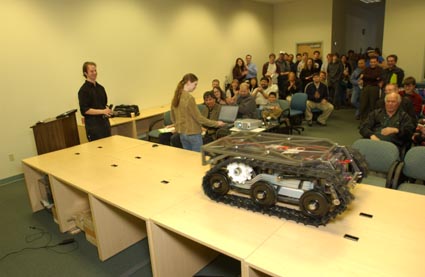 |
It works! When it finally moved, it actually received applause because it had been so much trouble. Not only was there the battery problem, but this was the third try since we got that working. First time, nothing happened because the safety kill switch on the speed controller was tripped, and the second time I'd forgotten to restore the master power link. Finally, however, we got it rolling across the tables, and everyone was delighted to see it work (especially us). |
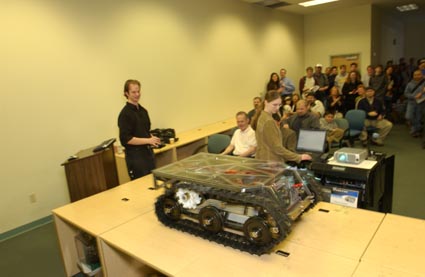 |
We drove it very, very slowly to the other end of the tables and then started doing a little turning. Everything was as slow and careful as we could manage. |
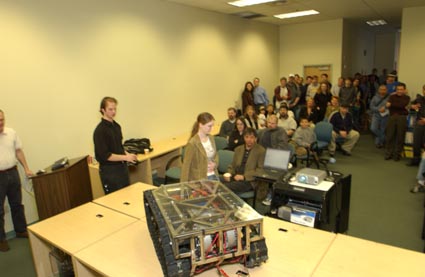 |
When we started turning I was a little worried that the dangling wires would get run over, but they cleared. |
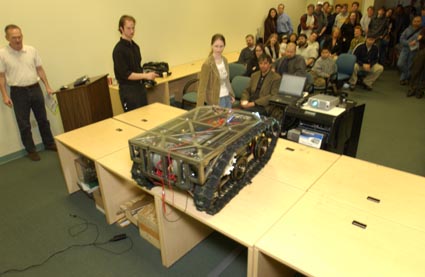 |
More driving pictures. It got a little close to the edge for comfort here, but it's actually not as precarious as it might seem. Keep in mind that roughly 90% of the weight is on the middle wheels, meaning that we'd have to roll back another full 16 inches before we were in real danger of running off the edge. |
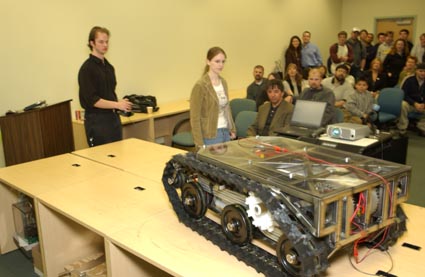 |
More driving... |
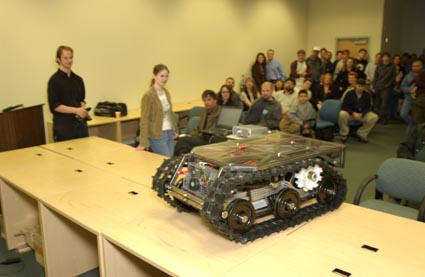 |
More... |
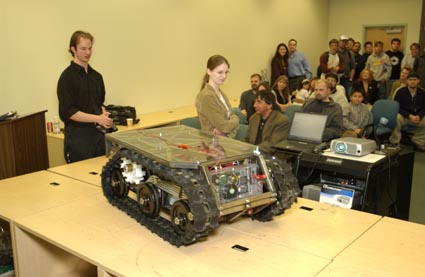 |
And even more driving. We don't have any video of this, but I figured a whole bunch of closely spaced pictures were the next best thing. If you want, you can print them out and make a flip-book. |
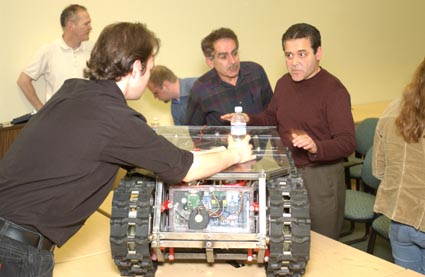 |
After the demonstration we chatted for a few minutes with some professors. In the burgundy is Dr. Wahab Abrous, the professor who taught my robotics course (among many others). We then rolled the robot back to the far end of the table to make way for the following presentations. |
The really bad news came later. We stayed through all of the following presentations, waited for the room to clear out, and then set about getting the robot down. We set up the wooden planks to drive down, and carefully lined everything up. We had to drive it down a little faster than I would have strictly liked, but it all went fairly well and we got the tracks back firmly on the ground. We were all done with the presentation, and, despite a few hitches, it had all went pretty well. We were feeling pretty good.
As we were driving to the door, Jake jumped on board and went for a ride. This is, by the way, completely within the determined application scope of the robot. I drove him around the room for a minute, one of the motors bogged down and started going "click-click-click," and smoke came pouring out of the speed controller. That's right. The very same, $500 controller that had arrived on my doorstep the day before and had been wired up exactly per the manufacturer's suggestions had just blown up.
I was upset.
I set about taking stuff apart, got the Lexan plating off, and removed the tracks. We rolled it out to the curb, loaded it into the van, and went home. Really, we were extremely fortunate with this timing -- if the controller was only going to survive for a day, that was the perfect day for it to survive through. We had it working through the demonstration, it was impressive, and we got our grades. In fact, in the end, we were even lucky that NPC screwed up the stock of this controller and didn't get it to us until the day before. If we'd gotten it when we should have, there's reasonably good odds that we would have blown it before the presentation.
This also gave us another positive result, believe it or not. The second controller blew in almost ideal conditions. It was not suddenly loaded, it was not regenerative breaking, it was not changing direction, and we had a log of every command sent to it (never more than 25 out of 127). This gave us a very powerful point to leverage against the manufacturer (you can see the discussion I had with them on their forum here (this is one of the threads that they deleted -- I rant about it a bit in last test's write-up)). In any case, suffice it to say that I complained. A lot.
And, as complaining often does, it paid off. Thanks to the work of the good people at NPC Robotics, I've been issued refunds on both AX2550 controllers. I'm still out all the time, shipping costs, wiring costs, cable costs, and high blood pressure that their product took, but I'm reasonably happy with the outcome. RoboteQ did cooperate (after a fashion), NPC took care of a lot of the work for me, and I got two $495 credits on my credit card.
With that situation ironed out, I spent a great deal of time researching a replacement controller. One thing that was a tremendous amount of help was a thread I started on the BattleBots Forum (it requests a login, but I believe guest entry is still permitted). Everyone there was a tremendous help, and after a bit of discussion I had it narrowed down to four major choices.
I was torn between the three best when David Moeller, the guy who runs Robot-Solutions LLC, sent me an e-mail. He said that he'd been following the thread and that he was willing to offer me a personal guarantee on a pair of MC1-HV controllers for my applications. That really made my day, and my new controllers should get here on Monday. They're the main reason my "Bottom Line" is over $800, but when you take into account the refund from the old AX2550's, I'm not doing too bad at all. The new controllers can handle more than four times more current than the old ones, and based on what everyone on the BattleBots forum had to say, should do the job just fine.
|
|